- Introduction
- The Basics Of Inductance
- What Is Inductance?
- Understanding the Unit of Inductance: Henry (H)
- Types of Inductors You’ll Encounter
- Common Misconceptions About Inductance
- Key Variables Influencing Inductance
- Core Material Properties
- Geometric Factors
- Environmental Impacts on Inductance
- Inductance in Real-World Applications
- Power Electronics and Inductance
- Inductance in RF Systems
- Specialty Applications in Industry
- Transformer Design
- Practical Inductance Measurement Techniques
- LCR Meters: The Industry Standard
- Oscilloscope-Based Inductance Measurement
- Advanced Impedance Analysis
- Advanced Techniques for Accurate Inductance Calculations
- Factoring in Real-World Effects
- Leveraging Simulation Tools
- Step-by-Step Example: Solenoid Inductance Calculation
- Tackling Common Inductance Issues
- Unreliable Measurements
- High-Frequency Effects
- Inductance in High-Frequency Design Challenges
- Parasitic Capacitance and Its Mitigation
- Q-Factor Optimization
- Skin Effect and Proximity Effect
- Emerging Trends in Inductance Design
- Miniaturized High-Power Inductors
- AI-Assisted Inductor Design
- Magnetic Nanomaterials
- Fast-Track Your Testing with Our Premium Refurbished Equipment
- Conclusion
- Whenever You’re Ready, Here Are 5 Ways We Can Help You
Have you ever designed a circuit, only to realize that your inductance calculations don’t quite match real-world performance?
Maybe you’ve spent hours tweaking components, trying to eliminate unexpected voltage drops or unwanted interference. Whether you’re fine-tuning a power supply or optimizing an RF filter, understanding inductance is key to getting your circuit to behave exactly as expected.
But here’s the challenge—inductance isn’t always straightforward. The formula looks simple on paper, yet real-world factors like core material saturation, parasitics, and frequency-dependent effects can throw off your calculations. And if your measurement tools aren’t precise, troubleshooting becomes a guessing game.
This guide cuts through the complexity. We’ll break down the inductance formula, explain the key variables that influence inductance, and show you how to apply it in real-world scenarios. We’ll also highlight how tools like LCR meters and network analyzers can help you measure and refine inductance values with confidence.
The Basics Of Inductance
Inductance plays a crucial role in electromagnetic induction, the principle behind transformers, motors, and generators and electronic systems.
According to the law of induction (also known as Faraday’s Law of Induction), a changing magnetic field induces a voltage in a conductor, which opposes the original current change. This opposition to change is the foundation of energy storage in inductors, power transfer in transformers, and the operation of electric devices.
This phenomenon is not just limited to large electrical systems—inductance influences everything from signal integrity in high-speed circuits to energy management in power electronics.
Understanding how inductance behaves in different conditions allows you to optimize circuit performance, reduce unwanted interference, and ensure efficient energy transfer across a wide range of applications.
For a fundamental understanding of inductance-related voltage changes, check out this guide on AC coupling.
What Is Inductance?
Inductance is a property of an electrical conductor that opposes changes in the electric current passing through it.
When current flows through a conductor, inductance generates a voltage that opposes sudden changes.
Whether you're optimizing a power supply for efficiency or fine-tuning an RF filter for signal integrity, understanding how inductance interacts with current in a coil and external electromagnetic fields is key to designing stable and reliable circuits.
The basic formula for calculating inductance is:
L = (N² * μ * A) / l
Where:
- L is inductance, measured in henries (H), the unit of inductance
- N is the number of turns of the coil
- μ is the permeability of the core material
- A is the cross-sectional area of the coil
- l is the length of the coil
Understanding the Unit of Inductance: Henry (H)
The henry (H) is the unit of inductance in the International System of Units (SI) named after American scientist Joseph Henry.
One henry is defined as the inductance of a circuit in which a change of one reciprocal ampere per second induces a voltage of one volt across the inductor.
Mathematically:
1 H = 1 V·s / A
In practical applications:
- Millihenries (mH) (1 mH = 10⁻³ H) and microhenries (µH) (1 µH = 10⁻⁶ H) are commonly used for smaller inductors in power supplies, RF circuits, and filters.
- Large inductors in transformers and industrial applications are often measured in henries.
Understanding the unit of inductance is crucial for selecting the right inductor for your circuit, ensuring that it properly manages current flow and electromagnetic interactions.
For a deeper understanding of how inductance relates to voltage, check out this guide on differential voltage relationships.
Types of Inductors You’ll Encounter
Inductors come in different types, each designed for specific applications. The core material greatly affects their behavior and efficiency:
- Air-Core Inductors: These do not contain a solid core, making them ideal for high-frequency RF applications where minimizing core losses is crucial.
- Ferrite-Core Inductors: These are commonly used in power supplies and filtering circuits. Their ferrite cores provide high permeability, allowing them to store more energy efficiently.
- Toroidal Inductors: These inductors have a ring-shaped core, reducing electromagnetic interference (EMI) and providing a compact design suited for efficient energy transfer.
Type | Core Material | Application | Advantages |
---|---|---|---|
Air-Core | None | High-frequency RF | Minimal core losses |
Ferrite-Core | Ferrite | Power supplies | High permeability |
Toroidal | Ferrite Powder | Compact designs | Low electromagnetic interference (EMI) |
Inductors aren’t limited to coiled wires—straight wires also exhibit inductance, particularly in high-frequency applications where distributed inductance becomes significant.
Common Misconceptions About Inductance
One of the most common myths is that "inductance doesn’t depend on material saturation." In reality, core materials can become saturated, which reduces their permeability and changes the expected inductance value.
Here are some practical tips to avoid common mistakes:
- Always account for core saturation: Choose core materials that match your application’s current requirements.
- Validate theoretical calculations with empirical tests: Real-world conditions can introduce variations that theoretical models may not predict.
- Recognize the limits of simplified formulas: Factors like temperature, frequency, and core material properties can impact inductance values.
For more foundational insights into how inductance affects circuit voltage, check out this guide on AC coupling.
Key Variables Influencing Inductance
Inductance isn't just about winding some wire around a core—it’s influenced by multiple factors, from material properties to environmental conditions.
If your calculations seem off, you might be overlooking one of these key variables. Understanding how inductance is affected by core materials, geometry, and environmental factors will help you design more reliable electric circuits and select the right components for your application.
For an in-depth look at how inductance interacts with frequency, check out this resource on frequency calculation.
Core Material Properties
The core material plays a critical role in determining an inductor’s efficiency and behavior. The permeability (μ) of a material dictates how easily it can support magnetic flux, directly impacting the inductance value.
However, permeability isn’t a fixed number—it changes based on factors like frequency and material saturation. When a core reaches saturation, it can no longer increase inductance, leading to non-linear circuit behavior. Additionally, hysteresis effects in certain materials cause energy losses, especially in applications requiring frequent current changes.
Here’s how different core materials compare:
Core Material | Permeability (μ) | Losses at High Frequencies | Applications |
Air | 1 (relative) | Minimal | High-frequency RF circuits |
Silicon Steel | High | Moderate | Transformers, power circuits |
Ferrite | Very high | Low | RF applications, filters |
For more on how inductance affects phase relationships in circuits, check out this guide on phase shift.
Geometric Factors
The physical design of an inductor significantly impacts its inductance. Three key geometric factors to consider are:
- Length (l): A longer coil reduces inductance because the magnetic field is spread out over a greater distance.
- Cross-sectional area (A): A larger cross-section increases inductance by allowing more magnetic flux.
- Number of turns (N): Inductance increases proportionally to the square of the number of turns.
For example:
- Solenoid Inductors: These are cylindrical and generate a strong magnetic field along their axis. They’re ideal for applications where a uniform field is needed.
- Toroidal Inductors: These have a ring-shaped core, which helps confine the magnetic field, reducing EMI and improving efficiency.
The right geometry depends on your application—whether you need higher inductance, minimal interference, or a compact design.
Environmental Impacts on Inductance
Inductance isn't static—it can change based on environmental conditions like temperature and humidity.
- Temperature effects: Core materials can lose permeability at high temperatures, reducing inductance.
- Humidity and moisture: Water can seep into the inductor’s insulation, affecting its electrical properties and leading to performance drift.
To mitigate these effects, consider the following design strategies:
- Use temperature-compensated materials: Some ferrite cores maintain stable permeability across a wide temperature range.
- Seal components to prevent moisture ingress: Protective coatings and enclosures can prevent environmental damage.
For more on how environmental factors impact electronic measurements, read this guide on dynamic range.
By accounting for these variables, you can ensure your inductors perform consistently across different operating conditions.
Inductance in Real-World Applications
Inductance is more than just a theoretical concept—it plays a crucial role in many industries, from power electronics to RF systems and specialized applications like automotive and medical devices.
Engineers rely on inductors for energy storage, signal filtering, and impedance matching, but real-world conditions often demand careful consideration beyond basic calculations.
For an example of how inductance affects circuit behavior, check out this guide on RLC circuits.
Power Electronics and Inductance
Inductors are essential in power electronics, particularly in filters, energy storage applications, and DC-DC converters.
They help smooth out voltage fluctuations, reduce noise, and manage power delivery efficiently. In digital circuits, inductance plays a critical role in managing transient voltages and ensuring stable signal transmission.
Key considerations when selecting an inductor for power circuits:
- Core selection to minimize losses: Using ferrite or powder cores helps reduce energy loss in high-power applications.
- Managing thermal effects during operation: Inductors can generate significant heat, so choosing materials with stable permeability across temperature ranges is critical.
- Saturation current rating: Ensure the inductor can handle peak currents without performance degradation.
For engineers designing power circuits, these factors determine whether an inductor will perform reliably over time.
Inductance in RF Systems
In radio frequency (RF) applications, inductance is key for impedance matching, frequency tuning, and signal filtering. RF circuits require precision, as small inductance variations can significantly impact performance.
Specification | Value Range | Use Case |
Inductance Value | 1 nH to 10 μH | RF filters, matching networks |
Quality Factor (Q) | 50–200 | High-frequency applications |
Frequency Range | Up to 3 GHz | RF communication systems |
For more on RF circuits and the role of inductors, see this RF applications guide.
Specialty Applications in Industry
Beyond power and RF applications, inductance plays a critical role in specialized industries.
Examples include:
- Automotive electronics: Inductors help suppress electromagnetic interference (EMI) in vehicle electronics, ensuring reliable communication between onboard systems.
- Medical devices: Inductance is used in implantable devices like pacemakers, where energy transfer must be efficient and precise.
- Industrial equipment: Many machines rely on inductive sensors for motion detection and safety systems.
Transformer Design
When two inductors are placed close together, a changing electric current in one can induce a voltage in the other. This principle, also known as mutual inductance, is the foundation of transformer operation and wireless energy transfer.
For a practical look at how inductors are used in transformers, check out this guide on transformer operation.
Practical Inductance Measurement Techniques
Measuring inductance accurately is essential for ensuring circuit performance, yet many engineers face challenges when translating theoretical values into real-world results.
Factors like frequency, temperature, and parasitic elements can affect measurements, making it important to use the right tools and techniques.
This section covers industry-standard methods for measuring inductance, including LCR meters, oscilloscopes with signal generators, and advanced impedance analyzers.
For a professional-grade inductance measurement tool, check out the Keysight E4980A Precision LCR Meter.
LCR Meters: The Industry Standard
LCR meters are the most reliable way to measure inductance, providing high accuracy across a wide range of frequencies.
These instruments apply an AC signal to the inductor and measure its response, giving precise readings of inductance (L), capacitance (C), and resistance (R).
How to Measure Inductance with an LCR Meter
- Select the correct test frequency: Higher frequencies reveal core losses and parasitic effects, so choose a setting that matches your application.
- Connect the inductor: Use Kelvin (4-wire) connections for better accuracy, especially for low-inductance measurements.
- Measure and interpret the results: The LCR meter will display the inductance value directly. Compare it to expected values and account for any deviations due to real-world factors.
Oscilloscope-Based Inductance Measurement
An oscilloscope with a signal generator provides an alternative method for measuring inductance, particularly when an LCR meter isn’t available. This approach requires measuring the phase shift between voltage and current in an AC circuit.
Step-by-Step Inductance Measurement Using an Oscilloscope
- Connect the inductor in series with a known resistor (typically 1Ω or 10Ω).
- Apply a sine wave from a signal generator at a known frequency (f).
- Measure the voltage across the inductor using an oscilloscope.
- Measure the current through the circuit (either directly with a current probe or indirectly by measuring voltage across the resistor).
- Calculate inductance using the phase shift method:
L = V / (2π f I)- V = voltage across the inductor
- f = applied signal frequency
- I =measured current
For a complete guide on this technique, check out this article on oscilloscope-based inductance measurement.
Additional resources:
Advanced Impedance Analysis
For high-frequency applications or complex inductor designs, an impedance analyzer provides deeper insights into inductance behavior. These tools can measure:
- Impedance across different frequencies to identify inductive reactance trends.
- Parasitic capacitance and resistance that affect inductor performance.
- Quality factor (Q) and loss characteristics, which are crucial in RF applications.
Interpreting Impedance Graphs
An impedance analyzer plots impedance vs. frequency, helping identify key trends such as:
- Inductive reactance increasing with frequency in a well-designed inductor.
- Resonant frequency, where parasitic capacitance cancels out inductance.
- Core losses, which appear as unexpected dips in the impedance curve.
To calculate complex impedance with inductance, use the Keysight Impedance Calculator.
For a deeper dive into impedance formulas and analysis, see this comprehensive impedance formula guide.
Using the right tools and methods ensures that your inductance measurements are accurate and reliable. Whether using an LCR meter, an oscilloscope, or an advanced impedance analyzer, understanding how to measure inductance effectively will help optimize your circuit designs.
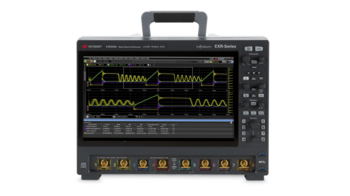
Advanced Techniques for Accurate Inductance Calculations
Inductance calculations can quickly become complex when real-world variables such as temperature, frequency, and material properties come into play.
While basic formulas provide a good starting point, engineers must account for practical effects that influence inductance in actual circuits.
This section explores advanced techniques for improving inductance calculations, leveraging simulation tools, and working through a real-world example.
Factoring in Real-World Effects
Inductance values can shift significantly due to environmental and operational factors. Ignoring these effects may lead to performance drift, increased losses, or circuit instability. Three major factors impact inductance in real applications:
- Temperature variations: Core materials can exhibit permeability changes at high temperatures, altering inductance values.
- Frequency-dependent effects: Skin effect and parasitic capacitance reduce effective inductance at higher frequencies.
- Material non-linearities: Magnetic saturation limits how much inductance a core can provide beyond a certain current threshold.
Corrections for Practical Scenarios
- High-frequency designs: Use Litz wire to reduce skin effect and maintain effective inductance.
- High-temperature environments: Select materials with low thermal sensitivity, such as temperature-stable ferrites.
- Avoiding core saturation: Choose cores with a higher saturation flux density or design for lower operating currents.
These adjustments ensure that inductors function consistently in varying conditions, leading to more reliable circuit performance.
Leveraging Simulation Tools
Modern electromagnetic simulation software allows engineers to model inductors with high precision before building physical prototypes. These tools help visualize magnetic fields, calculate inductance across different frequencies, and analyze losses due to resistance and parasitic capacitance.
One powerful option is Keysight Advanced Design System (ADS), which provides electromagnetic modeling for RF, microwave, and power electronics applications.
Comparison of Simulation Software Features
Software | Key Features | Best For |
---|---|---|
Keysight ADS | EM modeling, circuit simulation, S-parameter analysis | RF and power electronics |
Ansys Maxwell | Finite element analysis (FEA) for inductors | Complex 3D inductor modeling |
COMSOL Multiphysics | Multiphysics simulation with material properties | Thermal and structural analysis |
Simulation reduces costly design iterations by allowing engineers to refine inductance calculations digitally before physical testing.
Step-by-Step Example: Solenoid Inductance Calculation
To solidify the concept of inductance, let's go through a real calculation for a solenoid.
Given Parameters
- Number of turns (N) = 200
- Length of solenoid (l) = 50 cm = 0.5 m
- Cross-sectional area (A) = 10 cm² = 0.001 m²
- Permeability of free space (μ) = 4π × 10⁻⁷ H/m
Step 1: Apply the Solenoid Inductance Formula
The inductance L of a solenoid is given by:
L = (N² * μ * A) / l
Step 2: Substitute the Values
L = (200² × (4π × 10⁻⁷) × 0.001) / 0.5
L = (40000 × 1.256 × 10⁻⁶ × 0.001) / 0.5
L = (5.024 × 10⁻²) / 0.5
L = 0.1005 H (or 100.5 mH)
Advanced inductance calculations require engineers to factor in real-world effects, leverage simulation tools, and validate theoretical models with practical testing. By following these techniques, you can optimize inductor performance for demanding applications while minimizing costly design errors.
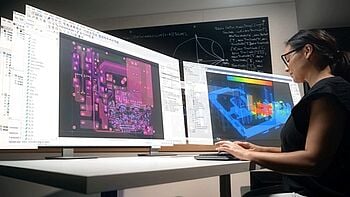
Tackling Common Inductance Issues
Even when calculations are correct, inductance-related issues can still arise due to real-world factors like measurement inaccuracies, parasitic effects, and environmental conditions.
Engineers often encounter challenges such as unreliable readings, high-frequency losses, and circuit loading effects that degrade performance.
This section provides practical solutions to common inductance problems, helping you improve measurement accuracy and optimize circuit behavior.
For a deeper understanding of circuit loading and its impact on inductance, see this guide on circuit loading.
Unreliable Measurements
Inductance measurements can be affected by stray capacitance, poor connections, and interference from external signals. These issues often lead to inconsistent or inaccurate readings, making troubleshooting difficult.
Common Causes of Unreliable Measurements
- Loose or poor connections: High-resistance connections can introduce unwanted noise and affect inductance readings.
- Stray capacitance: Unintended capacitance between circuit elements can distort inductance measurements.
- Electromagnetic interference (EMI): External signals can interfere with inductance readings, particularly in high-frequency circuits.
Troubleshooting Steps
- Check and tighten all connections: Ensure that probes and leads are properly secured.
- Use shielding to reduce interference: Enclose circuits in metal shielding or use twisted-pair wiring to minimize EMI.
- Calibrate measurement tools regularly: Instruments like LCR meters and oscilloscopes should be periodically recalibrated to maintain accuracy.
For more insights on maintaining measurement accuracy, explore this guide on signal integrity.
High-Frequency Effects
At high frequencies, inductors behave differently due to skin effect, parasitic capacitance, and other frequency-dependent losses. These effects can significantly impact circuit performance, leading to reduced efficiency or unexpected behavior.
Key High-Frequency Challenges and Solutions
Issue | Cause | Solution |
Skin Effect | Current crowding to conductor surface | Use Litz wire to distribute current evenly |
Parasitics | Interwinding capacitance in coils | Redesign winding configuration to reduce capacitance |
Eddy Currents | Circulating currents in conductive cores | Use laminated or powdered cores to minimize losses |
Resonance Peaks | Unintended LC resonance due to parasitics | Adjust circuit layout and component selection |
For engineers working with high-frequency circuits, it’s important to consider these effects early in the design process. Use the Keysight bandwidth calculator to analyze high-frequency performance limits, and refer to this guide on FFT analysis to better understand frequency domain characteristics.
Inductance in High-Frequency Design Challenges
At high frequencies, unwanted electromagnetic induction can introduce parasitic effects, leading to signal integrity issues in digital circuits. To minimize interference, optimizing winding structures and materials is crucial. Professionals working with RF applications, power electronics, and signal processing must also refine inductor performance to ensure efficiency and stability.
This section explores the biggest challenges in high-frequency inductor design and practical solutions to mitigate these issues.
Parasitic Capacitance and Its Mitigation
At high frequencies, inductors exhibit unintended interwinding capacitance, which can alter impedance characteristics, introduce unwanted resonances, and reduce performance. This parasitic effect is particularly problematic in RF circuits, where stable impedance matching is critical.
How Interwinding Capacitance Affects Performance
- Creates an unintended parallel LC resonance, leading to impedance peaks.
- Reduces effective inductance at higher frequencies, impacting signal integrity.
- Increases insertion loss, degrading overall circuit efficiency.
Solutions to Reduce Parasitic Capacitance
- Use distributed air gaps: Introducing small gaps in the winding structure reduces capacitance between turns.
- Optimize winding techniques: Using spaced or sectioned windings minimizes interwinding capacitance.
- Select high-Q materials: Ferrite cores with optimized permeability reduce losses while maintaining stable inductance.
By reducing parasitic capacitance, engineers can design inductors that maintain predictable behavior at high frequencies.
Q-Factor Optimization
The quality factor (Q) represents the efficiency of an inductor, defined as the ratio of reactance to resistance. A high-Q inductor exhibits lower energy loss, making it ideal for RF applications where precise impedance control is required.
How Q-Factor Affects High-Frequency Performance
- Higher Q means lower resistive losses and improved signal integrity.
- Low-Q inductors introduce unwanted damping, reducing circuit efficiency.
- RF circuits with poor Q experience degraded bandwidth and increased noise.
Ways to Improve Q-Factor in High-Frequency Inductors
- Select low-loss core materials: Ferrite and powdered iron cores offer better energy efficiency.
- Minimize resistive losses in windings: Use thicker wire or Litz wire to reduce AC resistance.
- Avoid sharp bends in winding layouts: Smooth, uniform coil structures minimize eddy current formation.
- Ensure proper shielding: Reducing interference prevents unnecessary energy dissipation.
By focusing on Q-factor optimization, engineers can achieve more efficient, stable, and high-performing RF circuits.
Skin Effect and Proximity Effect
At high frequencies, current tends to concentrate near the surface of a conductor due to the skin effect, increasing resistance and reducing efficiency. The proximity effect further worsens this by causing current redistribution due to nearby conductors.
How These Effects Impact Inductance
- Increased AC resistance: Less conductor area is available for current flow, raising resistive losses.
- Uneven current distribution: Higher-frequency signals experience distortion due to impedance variations.
- Greater heat generation: Increased resistance leads to excessive power dissipation.
Practical Solutions to Reduce Skin and Proximity Effects
- Use Litz wire: Multiple thin, insulated strands distribute current more evenly, reducing resistance.
- Space windings appropriately: Increasing coil spacing lowers the influence of proximity effects.
- Utilize high-permeability cores: These guide magnetic fields efficiently, reducing unwanted eddy currents.
By mitigating these effects, inductors can maintain better performance and efficiency in high-frequency applications.
Emerging Trends in Inductance Design
As technology advances, inductors are subject to the increasing demands of high-frequency applications, power efficiency, and miniaturization.
Engineers are now leveraging advanced materials, AI-driven optimizations, and nanotechnology to push the limits of inductance performance. These innovations are shaping the future of circuit design, enabling smaller, more efficient, and higher-performing inductors.
For more on modern measurement trends in inductance testing, check out the Keysight Network Analyzer Buying Guide.
Miniaturized High-Power Inductors
Traditionally, high-power inductors required bulky designs to handle large currents and magnetic fields. However, advancements in material science and core technology have led to compact, high-power inductors that maintain efficiency while reducing size.
Key Innovations in Miniaturized Inductor Design
- High-permeability composite materials: New ferrite and powdered iron composites enable high inductance in small footprints.
- Planar inductors: Printed circuit board (PCB) designs integrate inductance directly, reducing size and improving thermal dissipation.
- Thin-film magnetic materials: Deposited magnetic layers allow for ultra-compact inductors in high-density circuits.
These advancements are especially useful in automotive power electronics, IoT devices, and high-efficiency power converters, where space and efficiency are critical.
AI-Assisted Inductor Design
Artificial intelligence (AI) is revolutionizing inductor design by optimizing complex parameters that traditionally required extensive manual tuning. AI-driven simulations allow engineers to refine designs faster and improve overall performance.
How AI Enhances Inductor Design
- Optimizing Q-Factor: Machine learning models analyze vast datasets to recommend winding configurations and core materials that maximize efficiency.
- Thermal Efficiency Predictions: AI simulations predict heat dissipation patterns, enabling better thermal management strategies.
- Automated Parameter Adjustments: AI-powered design tools dynamically adjust core geometry, permeability, and layer thickness to achieve optimal performance.
AI-assisted tools reduce design cycles and improve performance consistency, making them essential for next-generation RF, power electronics, and signal processing applications.
Magnetic Nanomaterials
Nanotechnology is unlocking new possibilities in inductance by enhancing core materials at the atomic level. Magnetic nanomaterials offer superior permeability, lower core losses, and greater energy efficiency compared to traditional materials.
Benefits of Magnetic Nanomaterials in Inductor Design
- Higher magnetic permeability: Nanostructured ferrite and iron-based materials provide improved inductance density.
- Reduced hysteresis and eddy current losses: Nanoscale magnetic domains minimize energy dissipation at high frequencies.
- Improved thermal stability: Nanomaterials maintain consistent performance across extreme temperature variations.
These advancements are paving the way for more efficient wireless power transfer systems, high-speed data communication, and compact power inductors used in space-constrained electronics.
Fast-Track Your Testing with Our Premium Refurbished Equipment
Select up to 3 instruments to compare
Conclusion
Inductance is a fundamental yet complex aspect of circuit design, influencing everything from power electronics to RF systems. While basic formulas provide a foundation, real-world challenges such as parasitic effects, environmental variations, and high-frequency behaviors require deeper understanding and precise measurement techniques.
By applying advanced design strategies—factoring in material properties, leveraging simulation tools, and adopting cutting-edge technologies like AI-assisted modeling and nanomaterials—you can optimize inductance performance for even the most demanding applications.
Accurate inductance measurements require high-quality, reliable test equipment. Keysight’s premium used oscilloscopes, LCR meters, and network analyzers provide precision at a lower cost, helping engineers streamline development without sacrificing performance.
Equip your lab with industry-leading tools. Browse our premium used test equipment and get the precision you need—at the price you want.
Whenever You’re Ready, Here Are 5 Ways We Can Help You
- Browse our premium used network analyzers, oscilloscopes, signal analyzers and waveform generators.
- Call tech support US: 1 800 829-4444
Press #, then 2. Hours: 7am – 5pm MT, Mon– Fri - Talk to our sales support team by clicking the icon (bottom right corner) on every offer page
- Create an account to get price alerts and access to exclusive waitlists
- Talk to your account manager about your specific needs