- Introduction
- Core Concepts: What Defines a Magnetic Field?
- Visualization of Magnetic Fields
- Magnetic Field Strength and Direction
- Variables That Impact Magnetic Field Behavior
- Geometry and Distance
- Material Properties
- External Environmental Factors
- Magnetic Field Formulas Across Practical Applications
- Magnetic Fields in Rotating Machines
- Magnetic Interactions in Sensors
- Shielding and Magnetic Field Control
- Magnetic Field Formulas: Applied Physics for Engineers
- Calculating Magnetic Field Strength
- Field in Solenoids and Toroids
- Magnetic Flux and Inductance
- Measuring Magnetic Fields in Practice
- Magnetic Field Probes
- Oscilloscope-Based Measurements
- Solving Real-World Magnetic Field Challenges
- Reducing Magnetic Interference
- Designing for High-Frequency Applications
- Innovations in Magnetic Field Engineering
- Nanotechnology in Magnetic Materials
- Quantum Magnetic Sensors
- AI-Assisted Magnetic Design
- Invest in Precision with Keysight’s Certified Pre-Calibrated Equipment
- Conclusion
- Whenever You’re Ready, Here Are 5 Ways We Can Help You
You’ve designed a circuit, run the simulations, and everything checks out—until you test the prototype. Unexpected interference, overheating inductors, or inconsistent sensor readings throw your project off track. Sound familiar?
Magnetic fields are fundamental to electrical engineering, but they often behave in unpredictable ways. Whether you're working with solenoids, transformers, or wireless power systems, precise magnetic field calculations can mean the difference between an efficient design and one plagued by interference or losses.
This guide breaks down the essential formulas engineers need to predict and control magnetic fields. We’ll cover key variables, real-world applications, and the measurement techniques required for practical engineering work. By the end, you’ll have the tools to refine your designs and ensure your systems perform as expected.
Core Concepts: What Defines a Magnetic Field?
A magnetic field is the invisible force that surrounds electric currents and magnetic materials. It influences charged particles and determines how electrical devices function, from transformers and motors to wireless power transmission.
The magnetic field, represented with symbol B, represents both direction and strength, making it a fundamental concept in circuit design, energy systems, and modern communication technologies.
In electrical engineering, magnetic fields are crucial for inductive components, electromagnetic shielding, and sensor accuracy. Their behavior varies based on current flow, material properties, and external factors like frequency and temperature.
To measure and analyze magnetic fields, engineers rely on tools like magnetometers and oscilloscopes. For a deeper look into measurement techniques, check out this guide on magnetometers and fundamental electromagnetic field concepts.
Visualization of Magnetic Fields
Since magnetic fields are invisible, engineers use visualization tools to interpret their behavior. These tools help analyze field lines, which illustrate the strength and direction of magnetic influence around current-carrying wires, solenoids, and permanent magnets.
Common visualization methods include:
- Field pattern software: Simulates field behavior in different geometries.
- Graphical overlays in CAD tools: Helps design circuits with minimal electromagnetic interference.
- Simulation animations: Provides a dynamic view of changing field interactions over time.
These tools allow engineers to refine their designs and predict potential interference before building physical prototypes. Whether modeling magnetic shielding for a sensitive circuit or designing an efficient inductor, visual representation makes it easier to optimize performance.
Magnetic Field Strength and Direction
Magnetic fields are vector quantities, meaning they have both magnitude (strength) and direction. The strength of a magnetic field, denoted as B, depends on current, material properties, and distance from the source.
Here’s a quick comparison of magnetic field directional properties for common geometries.
Geometry | Directional Properties | Example Application |
Straight Wire | Circular field around the wire (right-hand rule) | Overhead power lines |
Solenoid | Uniform field inside, weaker outside | Transformers, inductors |
Toroid | Confined field within the core | High-efficiency inductors |
Understanding these directional properties helps engineers design efficient inductors, minimize EMI, and optimize sensor placement. For more insights into field direction and polarity, check out this guide on polarity in electronics and how differential voltage affects field measurements.
Variables That Impact Magnetic Field Behavior
Magnetic fields do not exist in isolation; they respond to their surroundings based on geometry, material properties, and external environmental factors.
These parameters must be considered when designing circuits, inductors, or electromagnetic shielding to ensure stable performance and minimize unwanted interference.
The shape and distance of conductors determine how the field distributes in space. Material properties, especially permeability, dictate how well a component can concentrate or shield a magnetic field. Meanwhile, environmental factors like temperature fluctuations or external electromagnetic interference can distort field behavior, leading to performance inconsistencies.
Understanding these influences allows engineers to optimize component placement, select the right materials, and implement shielding techniques that improve reliability.
The following sections break down each of these variables in detail, providing insights and practical design considerations.
Geometry and Distance
The geometry of a conductor or magnetic component significantly affects the distribution and strength of its magnetic field.
A straight wire, for instance, generates circular field lines around it, with strength decreasing as distance increases. In contrast, a solenoid concentrates its field inside the coil, creating a uniform region ideal for inductors and transformers.
Component spacing is just as critical. Magnetic field strength weakens with distance, following the inverse relationship defined by Ampère’s Law. Close proximity between components can lead to interference, whereas proper spacing can optimize performance and minimize losses.
Geometry | Field Strength Behavior | Best Applications |
Straight Wire | Decreases with 1/r | Overhead power lines |
Solenoid | Uniform inside, weaker outside | Transformers, inductors |
Toroid | Confined within the core | High-efficiency inductors |
Designing with geometry in mind allows engineers to control field distribution effectively. Choosing a solenoid over a straight wire, for example, helps concentrate the magnetic field where needed, reducing unintended interference.
Material Properties
Material selection plays a critical role in how a magnetic field behaves. A material’s permeability determines how effectively it can concentrate or block magnetic fields. High-permeability materials, like ferrites and mu-metal, enhance inductance and shielding performance, while low-permeability materials provide minimal magnetic influence.
Common materials used in engineering applications include:
- Ferrites: Used in EMI suppression and high-frequency transformers.
- Mu-metal: Highly effective for magnetic shielding in sensitive instruments.
- Silicon steel: Found in transformers and motors due to its low core loss.
Choosing the right material improves efficiency by guiding magnetic fields where they are needed and preventing unwanted interactions.
Explore how different materials impact magnetic performance in applications like transformers by referring to this guide on transformer operation. If you are dealing with advanced signal measurements, correlated double sampling offers insights into noise reduction techniques.
External Environmental Factors
Magnetic fields are highly sensitive to external influences, which can distort their behavior and reduce efficiency. Temperature fluctuations, humidity, and electromagnetic interference from nearby electronics can all impact performance.
Key mitigation strategies include:
- Use temperature-stable materials: Certain materials, like ferrites and silicon steel, maintain consistent permeability across varying temperatures.
- Enclose sensitive components in shielded housings: Metal enclosures or mu-metal shielding help block external interference.
- Optimize circuit layout: Proper grounding and spacing reduce unwanted magnetic coupling.
By accounting for environmental factors, you can improve the stability and reliability of magnetic systems. Designing for these challenges ensures that magnetic field performance remains consistent even in fluctuating operating conditions.
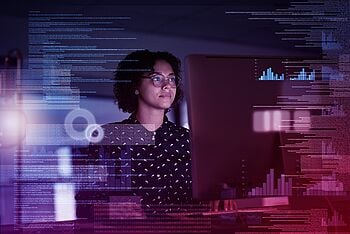
Magnetic Field Formulas Across Practical Applications
Magnetic fields play a critical role in many electrical and industrial applications, from motors and generators to sensors and shielding techniques.
Formulas are used to calculate field strength, direction, and interactions in real-world scenarios. Understanding these equations helps optimize designs for efficiency, minimize losses, and ensure reliable system performance.
Key formulas include those for magnetic field strength around conductors, induced voltage in rotating machines, and flux density in sensor applications. Each equation depends on variables like current, permeability, geometry, and environmental factors.
To apply these calculations effectively, follow these steps:
- Identify the source of the magnetic field (e.g., current-carrying wire, coil, or permanent magnet).
- Select the appropriate formula based on the system’s geometry.
- Input real-world parameters such as current, permeability, and distance.
- Use precision tools like Keysight’s impedance calculator to verify circuit parameters.
For more advanced applications, refer to this guide on electromagnetic energy calculations.
Magnetic Fields in Rotating Machines
Rotating machines, including motors and generators, rely on controlled magnetic fields to convert electrical energy into mechanical motion or vice versa. The strength and orientation of the magnetic field directly impact efficiency, torque output, and stability.
The magnetic field in a motor or generator is determined using Ampère’s Law and Faraday’s Law:
B = (μ * N * I) / L
where:
- B is the magnetic field strength,
- μ is the permeability of the core material,
- N is the number of turns in the coil,
- I is the current flowing through the coil,
- L is the length of the coil.
To optimize performance:
- Optimize winding patterns to ensure consistent magnetic flux distribution.
- Minimize core saturation by selecting appropriate core materials and avoiding excessive current.
- Maintain air gaps to prevent performance losses and ensure smooth operation.
For accurate field strength measurements, check this guide on amplitude measurement. To understand phase shifts in rotating fields, refer to this resource on phase shift analysis.
Magnetic Interactions in Sensors
Magnetic field sensors, such as Hall effect sensors and fluxgate magnetometers, detect and measure magnetic fields in a range of applications, from industrial automation to automotive systems. These sensors convert magnetic field variations into electrical signals, which can then be analyzed for precise control and monitoring.
Sensor Type | Sensitivity | Best Applications |
Hall Effect Sensor | Moderate | Automotive, current sensing |
Fluxgate Magnetometer | High | Precision navigation, geophysics |
Giant Magnetoresistance (GMR) Sensor | Very high | Hard drive read heads, medical imaging |
Hall effect sensors work by generating a voltage proportional to the perpendicular magnetic field component, while fluxgate magnetometers use alternating current to detect minute field variations with high precision.
For engineers working on signal processing, this guide on signal averaging can help improve data accuracy. Those measuring signal strength in communication networks may find this resource useful.
Shielding and Magnetic Field Control
Unwanted magnetic interference can degrade circuit performance, introduce noise, and lead to operational instability in sensitive electronics. Engineers use shielding materials and strategic design techniques to control and reduce electromagnetic interference (EMI).
Common shielding materials and their applications include:
- Mu-metal: High-frequency shielding for sensitive electronics and MRI rooms.
- Ferrite tiles: Used for suppressing RF interference in electronic enclosures.
- Copper mesh: Effective for low-frequency shielding in power electronics.
Other strategies for reducing unwanted magnetic interactions include:
- Placing critical components inside grounded metal enclosures to block external fields.
- Using twisted pair wiring to cancel out induced magnetic noise.
- Maintaining proper grounding to prevent unwanted coupling effects.
For more information on reducing unwanted interference, refer to this guide on coupling in electronics. Engineers working with sensitive circuit designs can also check out this resource on grounding.
Magnetic Field Formulas: Applied Physics for Engineers
Magnetic fields are essential in electrical engineering, affecting everything from power transmission to signal processing.
Engineers use precise formulas to calculate field strength, direction, and interactions with surrounding materials. These calculations help in designing efficient transformers, motors, and shielding systems.
This section presents key equations used to determine magnetic field properties in different configurations.
Calculating Magnetic Field Strength
The Biot-Savart Law describes the magnetic field produced by a small segment of current-carrying wire. It is given by:
B = (μ₀ / 4π) * (I * dℓ × r̂) / r²
where:
- B is the magnetic field strength,
- μ₀ is the permeability of free space (4π × 10⁻⁷ T·m/A),
- I is the current in the wire,
- dℓ is the infinitesimal length of the wire segment,
- r̂ is the unit vector from the wire to the point of observation,
- r is the distance from the wire to the observation point.
Example Calculation:
Find the magnetic field 5 cm away from an infinitely long wire carrying a current of 10 A.
Using the simplified form for an infinite wire:
B = (μ₀ * I) / (2πr)
Substituting values:
B = (4π × 10⁻⁷ T·m/A * 10 A) / (2π * 0.05 m)
B = 4 × 10⁻⁵ T
Thus, the field strength is 40 μT.
Field in Solenoids and Toroids
A solenoid is a coil of wire that generates a nearly uniform magnetic field inside its windings when carrying current. The magnetic field inside an ideal solenoid is:
B = μ₀ * μr * (N / L) * I
where:
- B is the magnetic field inside the solenoid,
- μ₀ is the permeability of free space,
- μr is the relative permeability of the core material,
- N is the number of turns,
- L is the length of the solenoid,
- I is the current.
A toroid, on the other hand, confines its magnetic field within a closed-loop core, reducing external interference. The field inside a toroid is given by:
B = (μ₀ * μr * N * I) / (2πr)
where r is the average radius of the toroid.
Comparison:
- Solenoids produce a strong, uniform field but have external leakage.
- Toroids confine the field within the core, making them ideal for efficient inductors and transformers.
Magnetic Flux and Inductance
Magnetic flux (Φ) represents the total magnetic field passing through a surface and is defined as:
Φ = B * A * cos(θ)
where:
- Φ is the magnetic flux in webers (Wb),
- B is the magnetic field strength in teslas (T),
- A is the area in square meters,
- θ is the angle between the field and the surface normal.
Inductance (L) quantifies a coil’s ability to generate an electromotive force (EMF) when current changes. It is given by:
L = (N² * μ * A) / L
where:
- N is the number of turns,
- μ is the permeability of the core,
- A is the cross-sectional area,
- L is the coil’s length.
Application | Role of Magnetic Flux and Inductance |
Transformers | Transfers energy between windings based on flux linkage. |
Motors | Converts electrical energy to mechanical motion. |
Inductors | Stores energy in magnetic fields to filter signals. |
Wireless Power | Uses resonant inductive coupling for efficient energy transfer. |
Understanding these relationships helps engineers optimize designs for energy efficiency, power regulation, and noise suppression in high-frequency applications.
Measuring Magnetic Fields in Practice
Accurate measurement of magnetic fields is essential in electrical engineering, from designing inductors and motors to diagnosing electromagnetic interference. Specialized tools such as magnetometers, field probes, and oscilloscopes help to quantify field strength and direction.
Interpreting results correctly requires an understanding of sensor limitations, environmental noise, and calibration techniques. Field measurements can vary based on sensor type, probe orientation, and surrounding conductive materials.
Common troubleshooting steps include:
- Verifying calibration and probe positioning to avoid misreadings.
- Shielding sensitive circuits to minimize interference from external fields.
- Using active probes for improved measurement accuracy.
For a comparison of different measurement tools, refer to this guide on spectrum analyzers vs. oscilloscopes.
Magnetic Field Probes
Magnetic field probes measure flux density and field strength in different frequency ranges. Selecting the right probe depends on sensitivity requirements and application needs.
Probe Type | Sensitivity | Best Use Case |
Fluxgate Sensor | High | Low-frequency field mapping |
Hall Effect Sensor | Moderate | Automotive applications |
Search Coil Probe | Low | High-frequency measurements |
Fluxgate sensors provide high sensitivity for low-frequency fields, making them ideal for geophysics and biomedical applications.
Hall effect sensors, commonly used in automotive and industrial systems, measure fields by detecting voltage changes perpendicular to the field direction. Search coil probes, suited for high-frequency applications, detect variations in time-varying magnetic fields.
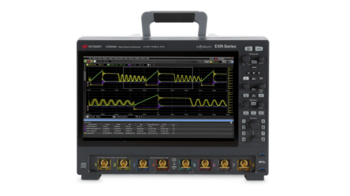
Oscilloscope-Based Measurements
Oscilloscopes are essential for analyzing time-varying magnetic fields, such as those in transformers, motors, and power electronics.
Steps for measuring magnetic fields using an oscilloscope:
- Select an appropriate probe based on the expected field strength and frequency.
- Connect the probe to the oscilloscope’s input channel.
- Position the probe near the magnetic source, ensuring proper orientation.
- Set the oscilloscope to an appropriate time base and voltage scale.
- Observe the waveform, adjusting the sensitivity to capture variations.
- Use filtering techniques to reduce external noise.
- Compare measured results with theoretical values to validate performance.
For engineers working with time-dependent signals, refer to this guide on amplitude measurement. To improve measurement accuracy, understanding dynamic range is critical.
Solving Real-World Magnetic Field Challenges
Interference, unintended field interactions, and frequency-dependent losses can degrade performance and introduce inefficiencies. Without proper mitigation strategies, systems can suffer from unwanted coupling, excessive heating, or signal distortions.
Common challenges include electromagnetic interference (EMI) in sensitive circuits, stray magnetic fields affecting precision sensors, and energy losses due to eddy currents in high-frequency applications. Addressing these issues requires selecting the right shielding materials, optimizing circuit layouts, and using frequency-specific design techniques.
The following sections outline solutions to these real-world problems, helping engineers improve performance and reliability.
Reducing Magnetic Interference
Magnetic interference can cause signal distortion, circuit malfunctions, and unwanted noise in sensitive electronics. Shielding techniques help contain and redirect magnetic fields, ensuring stable operation in power electronics, sensors, and wireless systems.
Common shielding materials and their applications include:
- Mu-metal: Provides high-permeability shielding for low-frequency magnetic fields.
- Ferrite tiles: Suppress radio-frequency interference in electronic enclosures.
- Copper or aluminum shielding: Effective for blocking low-frequency and static fields.
Best practices for minimizing magnetic interference:
- Use conductive enclosures: Metal housings help prevent external fields from penetrating sensitive components.
- Properly space components: Keeping high-current conductors and sensitive circuits apart reduces crosstalk.
- Optimize grounding techniques: Using a solid ground plane and minimizing ground loops reduces noise.
- Twist signal and power wires: This helps cancel out unwanted induced magnetic fields.
Applying these shielding techniques improves system reliability, especially in environments with strong electromagnetic fields.
Designing for High-Frequency Applications
High-frequency currents introduce additional challenges in circuit design due to the effects of skin depth and eddy currents. These phenomena impact the efficiency of inductors, transformers, and PCB traces, leading to signal degradation and energy loss.
Challenge | Cause | Solution |
Skin Effect | High-frequency currents concentrate near the conductor surface | Use Litz wire to distribute current evenly |
Eddy Currents | Circulating currents in conductive cores cause heat losses | Laminate the core to reduce eddy current loops |
Skin depth decreases as frequency increases, causing current to flow only on the outer surface of a conductor. This limits the effective cross-sectional area, increasing resistance and energy loss. Using Litz wire, which consists of multiple insulated strands, helps distribute current more evenly and reduces resistive losses.
Eddy currents occur when changing magnetic fields induce unwanted circulating currents in conductive materials, leading to power dissipation as heat. Laminated cores, made of thin insulated layers, interrupt these currents and significantly improve efficiency in transformers and high-frequency inductors.
Innovations in Magnetic Field Engineering
Advancements in materials science, quantum technology, and artificial intelligence are transforming how engineers design and optimize magnetic fields.
New nanostructured magnetic materials reduce losses in power electronics and motors. Quantum sensors provide unparalleled accuracy for medical imaging and space exploration. AI-driven design tools help engineers refine electromagnetic systems, minimizing interference and optimizing performance.
As these technologies evolve, engineers can integrate advanced analytical techniques, such as FFT analysis and frequency calculations, to improve real-world applications.
Nanotechnology in Magnetic Materials
Nanostructured magnetic materials are revolutionizing power electronics, transformers, and electric motors by reducing core losses and improving energy efficiency. By engineering materials at the atomic level, researchers can control properties such as permeability, coercivity, and saturation magnetization to enhance performance.
Key advancements include:
- Nano-grain soft magnetic materials: These materials reduce eddy current losses by limiting grain boundary resistance.
- High-frequency ferrites: Designed for minimal hysteresis loss, making them ideal for power conversion applications.
- Graphene-based magnetic coatings: Enhance conductivity and shielding properties in electronic enclosures.
These innovations allow for more compact, energy-efficient systems, reducing heat buildup and power dissipation. Industries such as renewable energy and consumer electronics benefit from improved transformer efficiency and higher-performance inductors. As nanomaterial development advances, engineers can expect even greater optimization in magnetic field applications.
Quantum Magnetic Sensors
Quantum magnetic sensors are redefining how engineers measure weak magnetic fields, offering unprecedented precision in applications like medical imaging, navigation, and space exploration. These sensors operate based on quantum mechanical principles such as spin alignment in atomic gases or superconducting quantum interference devices (SQUIDs).
Key technologies include:
- Optically pumped magnetometers (OPMs): Used in biomedical imaging, such as magnetoencephalography (MEG) for brain activity mapping.
- NV-center diamond sensors: Capable of measuring extremely small magnetic fluctuations at the atomic scale.
- SQUID sensors: Provide ultra-sensitive magnetic detection for deep-space probes and fundamental physics experiments.
These innovations are unlocking new possibilities in non-invasive diagnostics, underground mineral detection, and precise geophysical measurements. As quantum sensors become more accessible, engineers will gain tools that push the limits of traditional magnetic field measurements.
AI-Assisted Magnetic Design
Artificial intelligence is streamlining the design and optimization of electromagnetic systems by enabling rapid simulations and predictive modeling. AI-driven software tools analyze large datasets to identify patterns, improve efficiency, and minimize interference in magnetic field applications.
Applications of AI in magnetic design include:
- Topology optimization: AI refines component layouts to achieve maximum magnetic efficiency with minimal material use.
- Machine learning for predictive modeling: Algorithms predict electromagnetic interference (EMI) before prototype development.
- Automated parameter tuning: AI dynamically adjusts coil geometries, permeability, and shielding configurations for improved performance.
By integrating AI-driven solvers with traditional finite element analysis (FEA) tools, engineers can drastically reduce development time and improve system reliability. As AI continues to evolve, it will play a critical role in designing more efficient motors, wireless power transfer systems, and advanced sensing devices.
Invest in Precision with Keysight’s Certified Pre-Calibrated Equipment
Select up to 3 instruments to compare
Conclusion
Magnetic fields play a crucial role in electrical engineering, from power systems to high-frequency applications. Understanding the right formulas, measurement techniques, and shielding methods ensures efficiency and reliability.
As advancements in nanomaterials, quantum sensors, and AI-driven designs reshape the field, precision tools remain essential for accurate analysis and optimization.
For engineers who need reliable, high-performance test equipment without long lead times, Keysight Premium Used offers certified, pre-calibrated instruments at a great price. Check out Keysight’s Premium Used inventory to equip your lab with trusted measurement solutions.
Whenever You’re Ready, Here Are 5 Ways We Can Help You
- Browse our premium used network analyzers, oscilloscopes, signal analyzers and waveform generators.
- Call tech support US: 1 800 829-4444
Press #, then 2. Hours: 7am – 5pm MT, Mon– Fri - Talk to our sales support team by clicking the icon (bottom right corner) on every offer page
- Create an account to get price alerts and access to exclusive waitlists
- Talk to your account manager about your specific needs